This past weekend was the inaugural Stone Festival for Willowbank – an amazing weekend long event, the likes of which I’ve never seen before.
Apparently, there is a bit of a tradition among stone carvers of having events like this. The idea is for these carvers to get together as a community, enjoy interacting with each other (with perhaps even a bit of friendly competition), while promoting their craft to the wider public. They each start off with a block of stone, have a limited time to carve whatever they like, and at the end their pieces of work are auctioned off with the proceeds going to charity.
What an awesome idea!
The stone carving portion of the festival was organized by Danny Barber, a banker mason whose company Smith & Barber does a lot of work in Ottawa; and who is also our masonry instructor at Willowbank. He had organized this type of festival before, but this year decided to partner with Willowbank to do something a little bit different.
And of course, Willowbank being the type of place it is, couldn’t just do what had been done before. We had to up the game, and what we did ended up being very special indeed.
You see, stone isn’t just good for carving, or cutting into blocks and sticking it together with mortar to build with. It can also be simply stacked up, without mortar, to build with too. And that’s where some of the world’s best dry stone wallers came into the picture…
For the past couple of years, Willowbank students have been working on the construction of a substantial timber frame building. It was originally going to be a ‘chipping shed’ for our masonry classes. I believe the idea was just an open frame with a roof to keep the elements off us. But someone seems to have come up with a much better plan for that structure – a Blacksmith’s Shop (which they’re calling the ‘Forge Studio’). And even better than the re-allocation of space for smithing, is the decision to add walls. Stone walls. Dry stone walls, to be precise.
Yes, Willowbank is getting a heavy (mostly oak) timber framed blacksmiths shop, which will be one of only a handful of dry stone buildings in North America. And the dry stone portion of that building, was substantially built this past weekend during the stone festival.
I’m nowhere near good enough at writing, to effectively express how totally awesome this building is, or how excited I am about this shop being built.
The Stone Festival had (I believe) 24 or 25 carvers working all day Saturday and Sunday, carving some really amazing things. Meanwhile, Willowbank’s dry stone walling instructor Dean McLellan, along with a few Master wallers from Great Britain (from the DSWA), taught dry stone walling courses while a team of 15 wallers worked on the new building.
While all of these highly skilled masons plied their crafts, there were other festival-like events filling out the schedule for the weekend. We had a ‘Flea’ going on Saturday, where several vendors were selling cool ‘stuff’ (antiques and such), a bunch of kids were being kept occupied with face painting and other activities, while some tasty food and beverage was being sold – and yes, some of that beverage was of the alcoholic variety ;-) .
On the Saturday evening, sleepy, quiet little Queenston came alive with a street dance of all things. Probably the most activity it’s seen since the war of 1812. Okay, that’s an exaggeration – but not much of one.
Sunday evening was the ‘Stone Festival Party’, where all of the carvers work was auctioned off. This is where I came in. You see, this event had an ‘elemental’ theme to it. They wanted to showcase stone, glass, wood, iron and the like. And so when this was being planned out, I was asked if I would be willing to do a blacksmithing demo as part of the evenings entertainment. I was happy to do so, but wasn’t going to set up all that equipment for just a few hours. Instead I set up early Saturday morning, and forged all weekend (along with one of our new 1st year students, Tyson, who is also an avid blacksmith).
Saturday was the longest single stretch I’d ever forged for. I was set-up around 7:00 am and went straight through to almost 8:00 pm. There was such a large crowd around me the entire time that I never found time for a break. At one point Tyson went on an epic quest to find us some food.
Sunday was a slightly later start, but was also really busy. The real excitement was Sunday evening during the party.
During most of the weekend, I was busy at my forge, the carvers were busy at their benches, and the wallers were busily working at lifting and stacking very heavy things to make us a smithy! There was this great sound as we were all hammering and chiseling away at our various projects. But as the carvers finished, and the wallers ran out of daylight, I finally got to meet all of these fantastic people as they started wandering towards the forge.
What I didn’t realize before, is that most of us who enjoy smacking at things with a hammer, have a lot in common. And the mason’s all seemed to love the blacksmithing. At one point I probably had 20 or more of them crowded around. Many of whom said they ‘always wanted to try this’ (smithing), and so of course I had to oblige them.
By 9:30 Sunday night, I was standing around in the pitch black, under a tree (in the pouring rain) talking a bunch of masons through making their first basic smithing projects. Despite the late hour, and less than ideal weather, I was having the most fun I’ve ever had working at a forge.

I’m going to need a few days to recover, as I’m exhausted, but would do this all over again in a heartbeat. I’m really hoping that this first Willowbank Stone Festival, is the first of many!
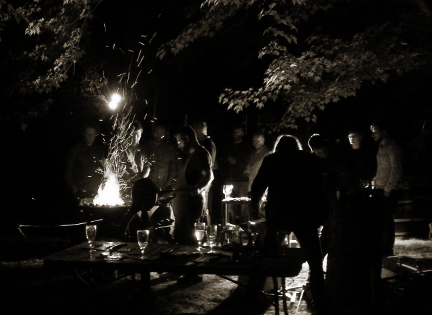
You must be logged in to post a comment.